The construction landscape is evolving, and a leading catalyst for this change is the growing adoption of prefabricated construction. This innovative building method, where sections of a structure are manufactured off-site and then transported to the construction site for assembly, is transforming the way we build and live. The rising trend of prefabricated construction brings with it a host of benefits, but it’s not without its challenges. This blog post explores both aspects in-depth.
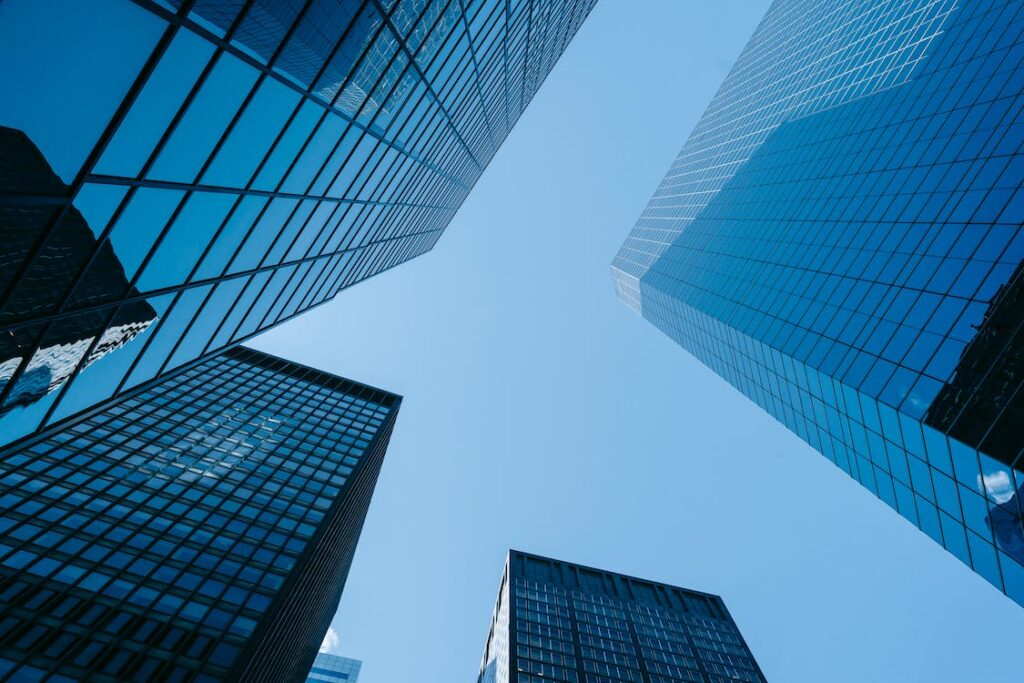
Benefits of Prefabricated Construction
Efficiency and Speed: One of the most compelling advantages of prefabricated construction is the significant reduction in build time. Since components are manufactured off-site in a controlled environment, the process isn’t affected by weather or site conditions, enabling concurrent on-site and off-site construction. Additionally, the use of automation and repeatable processes in a factory setting can boost efficiency, significantly accelerating the production time of various elements.
Cost Savings: Prefabrication can lead to substantial cost savings. Efficient production methods, minimal waste, and a streamlined timeline all contribute to a lower cost. Furthermore, there’s less uncertainty in prefabricated construction, leading to more accurate project budgeting and reducing the risk of unexpected costs.
Quality Control: Prefabricated components are built in a controlled factory environment, using detailed plans and precise machinery. This setting enables rigorous quality checks, leading to high-quality components with greater durability and less likelihood of faults, ultimately improving the longevity of the constructed buildings.
Reduced Waste and Environmental Impact: Prefabrication supports sustainable construction practices. The controlled manufacturing process results in minimal waste, and leftover materials can be easily recycled. Additionally, since most of the construction occurs off-site, there’s less site disruption, noise, and air pollution, minimising the project’s environmental footprint.
Safer Work Conditions: Safety is a top concern in the construction industry, and prefabrication offers significant safety improvements. The factory-controlled process reduces the likelihood of on-site accidents, and the reduction in on-site construction activities means less exposure to adverse weather conditions and site-related hazards for workers.
Challenges of Prefabricated Construction
Despite the compelling benefits, prefabricated construction isn’t without challenges.
Perception and Awareness: Many people still associate prefabrication with low-quality, cookie-cutter designs. While this is no longer the case, changing these ingrained perceptions takes time. Additionally, a lack of awareness about the benefits of prefabricated construction among consumers and some industry professionals can slow its adoption.
Upfront Costs: Prefabricated construction often requires a higher initial investment compared to traditional construction methods. The costs of setting up or accessing a manufacturing facility, as well as the need for specialised machinery and skilled labour, can be prohibitive for some projects.
Design Limitations: While prefabrication offers a variety of design options, it may not be suitable for all architectural styles or customised designs. Some complex or unique design elements may be difficult or impossible to produce in a factory setting, limiting the design flexibility.
Transportation and Logistical Challenges: Transporting the prefabricated modules from the factory to the construction site can be a challenge, especially for large components. It requires careful planning and coordination, and in some cases, special transport permits. Additionally, the site must be prepared to receive and install the components upon arrival, necessitating precise scheduling.
Regulatory Hurdles: Different regions have various building codes and regulations, which can create complications for prefabricated construction. Some codes may not account for the unique aspects of this construction method, requiring manufacturers and builders to navigate a complex regulatory landscape.
The rise of prefabricated construction represents a promising trend towards more sustainable, efficient, and safe building practices. However, to fully harness its potential, the industry must address the associated challenges. This involves educating consumers and professionals about its benefits, investing in the necessary equipment and skills, innovating in design capabilities, and working with regulatory bodies to update building codes.
As we look to the future of construction, it’s clear that prefabrication will play a significant role. The journey may be fraught with challenges, but the benefits make it a worthwhile pursuit. By embracing prefabrication, we can pave the way for a more efficient, sustainable, and resilient construction industry.
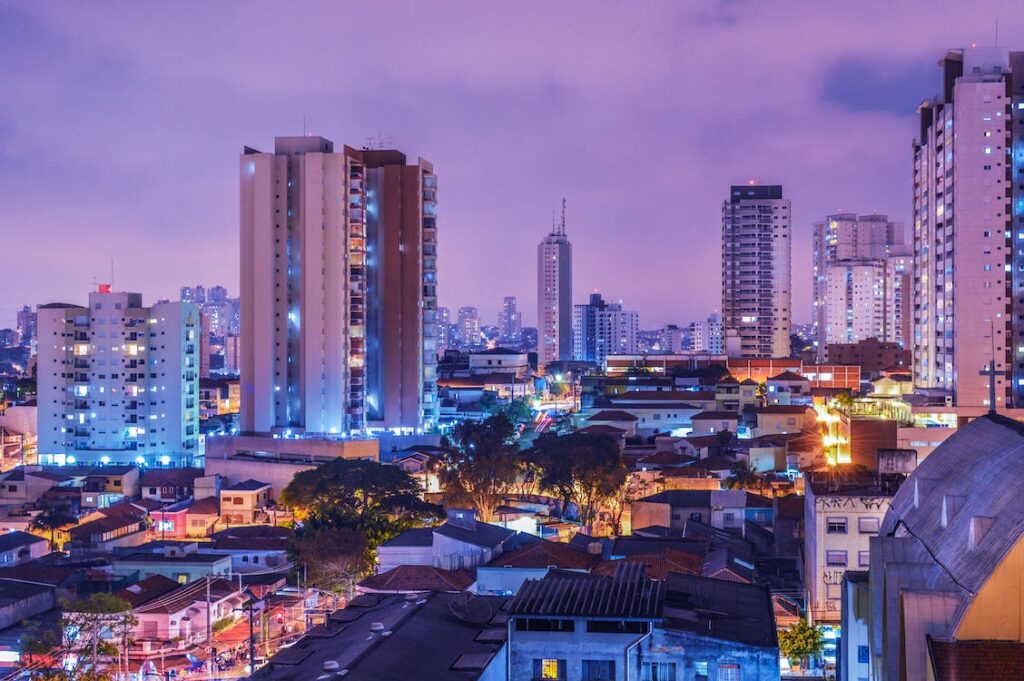
Potential Applications of Prefabricated Construction
Prefabricated construction holds immense potential in various construction sectors. In residential construction, it can be effectively used for single-family homes, multi-family apartments, and affordable housing projects. Given the speed and cost-efficiency, it is particularly suited to large-scale housing projects where uniformity in design is a benefit, not a limitation.
The commercial sector can also leverage prefabrication for office buildings, retail outlets, and hospitality establishments. With careful planning, businesses can minimise downtime during construction, ensuring their operations are not significantly disrupted.
Prefabrication is also a viable solution for emergency and temporary structures, such as disaster relief shelters or medical facilities during a crisis. The speed of construction can make a crucial difference in such situations, providing immediate shelter and relief to those in need.
In the public sector, prefabrication can be utilised for schools, hospitals, and other public facilities. It offers an efficient way to construct high-quality public infrastructure within a shorter timeline, ultimately benefiting the community.
Future Prospects of Prefabricated Construction
As technology continues to evolve, we can expect even more advancements in prefabricated construction. For instance, the integration of digital technologies like Building Information Modeling (BIM) can streamline the design and manufacturing process, enhancing precision and efficiency.
Furthermore, automation and robotics in manufacturing facilities will continue to drive up productivity while reducing costs. As these technologies become more widespread, we could see more complex and unique designs being realised through prefabrication.
Additionally, as sustainability becomes a more pressing concern globally, the green credentials of prefabricated construction will become increasingly important. The efficient use of materials, coupled with the potential for integrating renewable energy sources and energy-efficient designs, will make prefabrication an attractive choice for eco-conscious builders and consumers.
Integration with Emerging Trends
The potential of prefabricated construction is magnified when integrated with other emerging trends in the construction industry. For example, digital technologies, such as virtual reality (VR) and augmented reality (AR), can be used to enhance the design process, enabling stakeholders to visualise and tweak the design before it goes into production. This can increase efficiency, reduce errors, and lead to better outcomes.
Furthermore, the rise of smart homes and the Internet of Things (IoT) presents exciting opportunities for prefabricated construction. Smart devices and systems can be integrated during the manufacturing process, making the installation more seamless and ensuring better performance.
Role of Education and Training
For prefabrication to become mainstream, it’s crucial to invest in education and training. The construction industry needs professionals who understand the unique aspects of prefabricated construction and can effectively manage such projects.
Training programs can equip construction workers with the skills needed to assemble prefabricated components. Similarly, courses for architects and engineers can focus on designing for prefabrication, ensuring they can fully leverage its benefits.
Global Scope of Prefabrication
Prefabrication is a global trend, and its adoption varies across the world. In some countries, like Sweden and Japan, prefabricated construction accounts for a significant proportion of new builds. These countries serve as excellent examples of what can be achieved with widespread adoption of prefabrication.
In contrast, in countries where prefabrication is still in its early stages, there’s a tremendous opportunity for growth. As more success stories emerge and as the benefits become more evident, we can expect to see a rapid increase in the adoption of prefabrication.
The rising trend of prefabricated construction is poised to reshape the global construction industry. While it presents its own set of challenges, the potential benefits in terms of efficiency, cost, quality, sustainability, and safety are game-changing. By embracing this trend and working towards overcoming the obstacles, the construction industry can take a giant leap forward, delivering better buildings faster and at a lower cost. Prefabricated construction, no doubt, holds the key to a more efficient and sustainable future of construction.
As the construction industry embraces trends like prefabrication, it’s critical to use management tools that support these methods. Wunderbuild is a comprehensive construction management software designed to handle the intricacies of modern construction projects. Whether it’s job management, task scheduling, cost control, or effective collaboration among teams, Wunderbuild streamlines it all. While prefabrication may simplify the construction process, managing such projects can still be complex. That’s where Wunderbuild comes into play, enhancing coordination, improving productivity, and ensuring that your project runs smoothly from beginning to end. Explore the possibilities with Wunderbuild here.