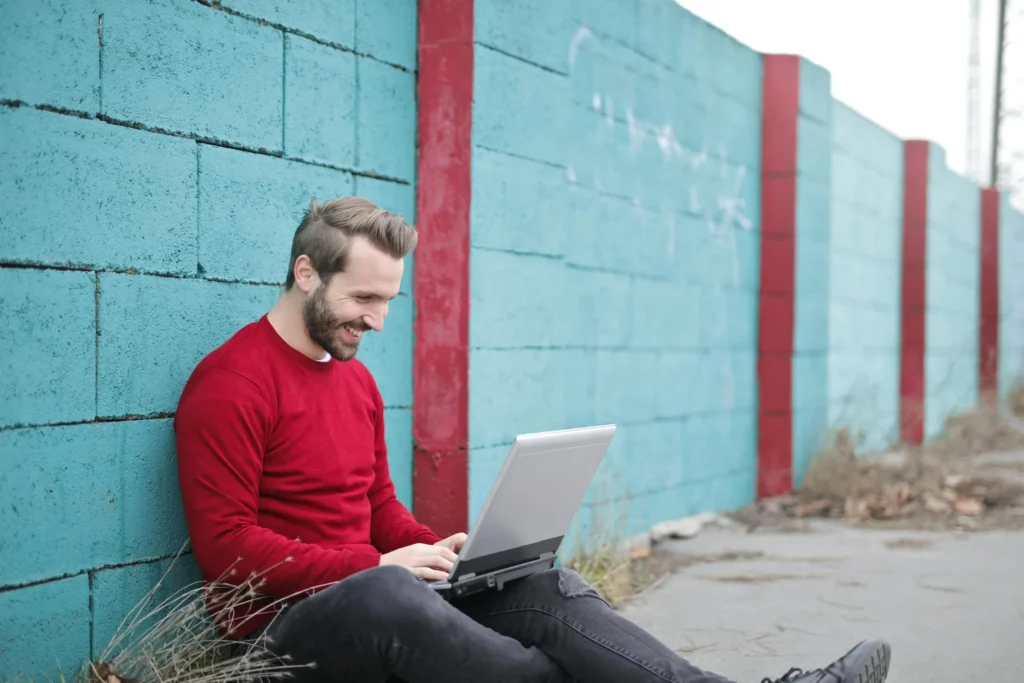
The construction industry is undergoing a digital transformation, with innovative technologies reshaping traditional processes. One of the most impactful advancements in recent years is the emergence of Digital Twins. This technology enables real-time monitoring, simulation, and analysis of construction projects, significantly enhancing efficiency, reducing costs, and improving decision-making. As construction projects become increasingly complex, Digital Twins provide an integrated, data-driven approach to planning and execution.
Construction projects have historically been plagued by inefficiencies, cost overruns, and unforeseen delays. Traditional planning and execution methods often lack the agility needed to adapt to real-world challenges in real time. Digital Twins address these pain points by offering an intelligent, connected ecosystem where stakeholders can visualise, simulate, and optimise every aspect of a project from start to finish. By integrating physical and digital elements, Digital Twins not only enhance project transparency but also enable a proactive approach to problem-solving, ultimately leading to safer and more sustainable construction practices.
This article explores how Digital Twins are revolutionising construction planning and execution, the key benefits they offer, and the challenges involved in their implementation.
What Is a Digital Twin?
A Digital Twin is a virtual replica of a physical asset, system, or process that integrates real-time data, historical records, and predictive analytics to optimise performance. In construction, Digital Twins are created by combining Building Information Modeling (BIM), Internet of Things (IoT) sensors, artificial intelligence (AI), and data analytics.
These digital representations continuously update based on live inputs from the physical structure, providing an accurate, real-time view of the construction site and its evolving conditions. Digital Twins enable stakeholders to simulate, predict, and optimise project performance before and during construction.
Unlike static 3D models, Digital Twins are dynamic and evolve over time. They integrate data from multiple sources, including drones, sensors, and project management tools, allowing construction professionals to analyze trends and make data-driven decisions. By creating a virtual copy of a construction site, project managers can test different scenarios, forecast potential risks, and refine workflows for maximum efficiency. This level of insight empowers teams to minimise waste, reduce rework, and streamline project timelines.
How Digital Twins Are Transforming Construction Planning
1. Enhanced Design and Visualisation
Traditional construction planning relies heavily on 2D blueprints and 3D models, which can sometimes fail to provide a comprehensive understanding of the project. Digital Twins, however, offer dynamic, interactive simulations that allow engineers, architects, and project managers to visualise the project in an immersive, real-world context. This enhances decision-making and improves stakeholder collaboration.
For instance, instead of relying solely on architectural drawings, teams can use Digital Twins to conduct virtual walkthroughs of a building before construction even begins. This level of visualisation enables stakeholders to detect design inconsistencies, assess spatial relationships, and make informed design modifications early in the process. Additionally, these models can be shared with clients and investors, fostering better communication and alignment among all parties involved.
2. Improved Risk Management
One of the biggest challenges in construction is managing risks related to design flaws, material shortages, and site conditions. Construction projects are often plagued by unforeseen obstacles, such as unexpected soil conditions, inaccurate material estimations, and last-minute design modifications. These risks can lead to project delays, increased costs, and compromised structural integrity. Digital Twins help mitigate these risks by providing an intelligent, data-driven approach to construction management.
Firstly, Digital Twins simulate construction scenarios to identify potential bottlenecks before breaking ground. By creating a real-time, virtual model of the project, construction teams can test various building sequences, logistics plans, and resource allocations before executing them in the real world. This predictive capability allows project managers to anticipate issues such as congestion on-site, inefficient workflows, and delays due to dependencies between tasks. For example, if a simulation reveals that a particular phase of construction is likely to experience delays due to equipment congestion, project managers can adjust schedules, allocate additional resources, or redesign the sequence of activities to optimise efficiency.
Additionally, Digital Twins play a crucial role in analyzing environmental impacts such as weather conditions, soil stability, and site accessibility. Construction projects are highly dependent on external factors, and even slight changes in temperature, humidity, or wind speed can affect material properties and construction timelines. Digital Twins can integrate real-time meteorological data and historical weather patterns to predict how weather conditions will impact construction activities. For instance, if a Digital Twin identifies that heavy rainfall is expected during a crucial phase of concrete pouring, project managers can reschedule the activity to avoid quality issues related to water infiltration. Similarly, soil conditions can be analyzed using geotechnical data, allowing engineers to assess the risk of foundation instability or landslides before beginning excavation. This level of foresight minimises unexpected site challenges, reducing costly adjustments and ensuring structural integrity from the ground up.
Another significant advantage of Digital Twins is their ability to detect clashes and conflicts in design early on, which helps reduce costly rework. In traditional construction, errors and inconsistencies between architectural, structural, and mechanical plans often go unnoticed until construction is well underway. This can lead to expensive modifications, material waste, and extended timelines. Digital Twins eliminate this issue by continuously cross-referencing design elements in real-time, ensuring that all components align perfectly before construction begins. Using AI-driven clash detection, project teams can identify conflicts such as HVAC ducts interfering with load-bearing beams or electrical conduits overlapping with plumbing systems. By resolving these discrepancies in the virtual environment, teams can make design modifications without disrupting physical construction, significantly reducing errors and rework.
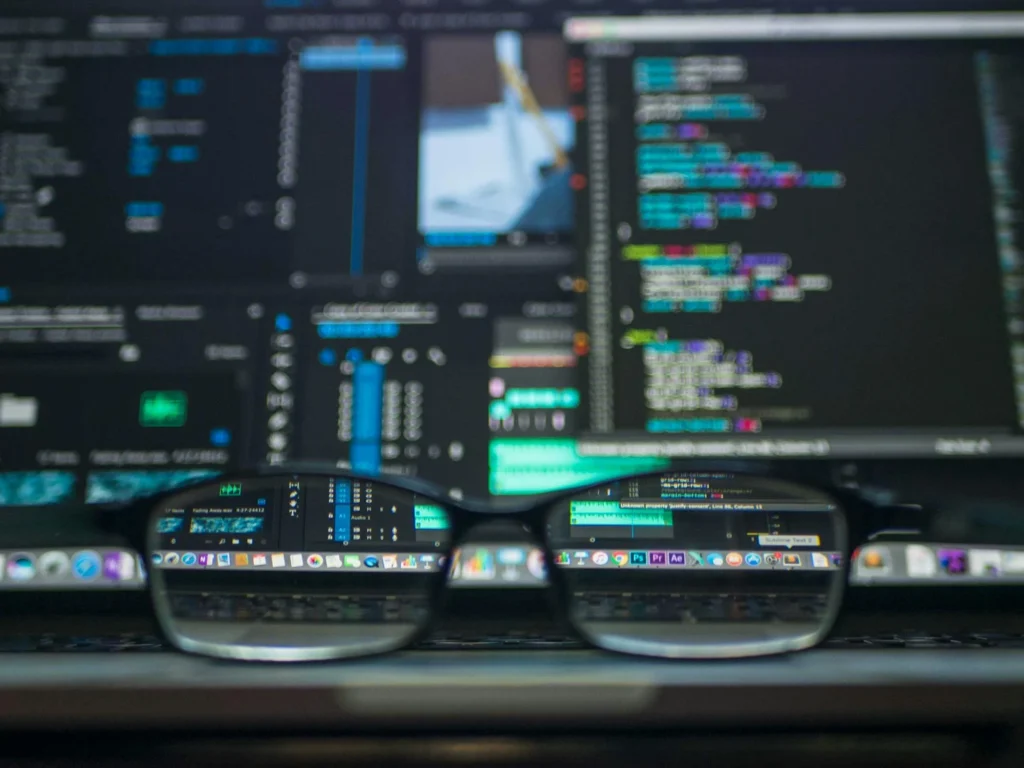
Beyond technical aspects, Digital Twins also improve risk management in procurement and supply chain logistics. Material shortages and supply chain disruptions can derail a project’s timeline and inflate costs. Digital Twins integrate procurement data with real-time construction progress, ensuring that materials arrive on-site precisely when needed. This “just-in-time” approach minimises storage costs, prevents material degradation due to prolonged exposure, and reduces the risk of shortages or excess inventory. Moreover, predictive analytics help project managers forecast demand for materials based on evolving project conditions, allowing them to make informed purchasing decisions and negotiate better deals with suppliers.
By leveraging predictive analytics, construction teams can foresee issues such as foundation instability or supply chain disruptions, allowing them to take preventive measures in advance. This proactive risk management approach can significantly reduce project delays and unexpected expenses.
3. Data-Driven Decision-Making
Digital Twins collect and analyze real-time and historical data, enabling data-driven decision-making. By leveraging AI and machine learning, construction teams can:
- Predict material consumption and optimise procurement.
- Monitor workforce productivity and safety compliance.
- Adjust schedules dynamically to accommodate unforeseen delays.
The ability to make informed decisions based on accurate, real-time data is a game-changer for construction firms. Rather than reacting to problems after they occur, project managers can anticipate challenges and implement solutions before they escalate. Additionally, real-time data insights contribute to improved budgeting, as firms can allocate resources more efficiently and prevent cost overruns.
4. Sustainable and Smart Construction
With the growing emphasis on sustainability, Digital Twins help optimise resource utilisation and reduce construction waste. By analyzing data on material efficiency, energy consumption, and environmental impact, project managers can make more informed choices to minimise their carbon footprint.
For example, Digital Twins can simulate different building materials and construction techniques to determine the most eco-friendly and cost-effective options. By monitoring energy usage throughout a building’s lifecycle, facility managers can also optimise heating, cooling, and lighting systems to minimise operational costs and environmental impact.
Digital Twins in Construction Execution
1. Real-Time Monitoring and Site Management
IoT-enabled sensors embedded in machinery, materials, and site infrastructure collect real-time data on temperature, humidity, structural integrity, and equipment performance. This data feeds into the Digital Twin, providing a live, remote overview of the construction site. Project managers can:
- Monitor work progress and detect deviations from the schedule.
- Identify safety hazards and take immediate action.
- Optimise the use of resources and workforce allocation.
2. Predictive Maintenance and Asset Management
Digital Twins are particularly beneficial in monitoring construction equipment and infrastructure integrity. By analyzing sensor data, AI can predict when machines or materials will fail, allowing for proactive maintenance. This reduces downtime, extends the lifespan of assets, and minimises unexpected costs.
3. Enhanced Collaboration Across Teams
Construction projects involve multiple stakeholders, including architects, engineers, contractors, and investors. Digital Twins serve as a centralised platform for collaboration, ensuring that all parties have access to the same up-to-date project data. This minimises communication gaps and enhances coordination between different teams.
4. Quality Control and Compliance
Ensuring compliance with building codes and safety regulations is critical in construction. Digital Twins help by:
- Automating quality checks through AI-powered image recognition.
- Comparing completed work against design specifications in real time.
- Generating reports for regulatory compliance and audits.
Challenges in Implementing Digital Twins
Despite their advantages, Digital Twins face challenges such as high implementation costs, data security concerns, and interoperability issues. However, as the technology matures and adoption rates increase, these barriers are expected to decrease.
Future of Digital Twins in Construction
With advancements in AI, cloud computing, and 5G connectivity, Digital Twins will become even more sophisticated and accessible. Some emerging trends include:
- AI-driven automation for predictive analytics and autonomous construction.
- Integration with augmented reality (AR) and virtual reality (VR) for immersive project visualisation.
- Smart cities and infrastructure projects leveraging Digital Twins for long-term asset management.
Digital Twins are revolutionising the construction industry by bridging the gap between physical and digital project management. From enhanced planning and risk mitigation to real-time execution and predictive maintenance, this technology is transforming the way construction projects are designed, executed, and managed.
As the industry continues to embrace digital transformation, the widespread adoption of Digital Twins will pave the way for smarter, more efficient, and sustainable construction practices. Companies that invest in Digital Twin technology today will gain a competitive edge in the future of construction.
In today’s construction landscape, efficiency and accuracy are paramount. Construction management software, like Wunderbuild, revolutionises project handling by centralising tasks, from scheduling and budget management to communication and document control. This integration enhances productivity and ensures projects are completed on time and within budget, making it an essential tool for modern construction professionals. Embrace Wunderbuild here to begin streamlining your construction processes and boost your project’s profitability.