In the world of construction, finding ways to maximise efficiency and control costs without compromising quality is crucial for success. With increasing competition, fluctuating material prices, and evolving client expectations, it is essential for builders and construction professionals to adopt cost-effective strategies that optimise resources, streamline processes, and deliver high-quality results. In this blog, we will explore a range of proven cost-effective construction strategies that can help maximise efficiency, reduce expenses, and ensure quality outcomes. From careful project planning to smart material selection, innovative technologies, and effective project management, we will delve into practical approaches that can be implemented to achieve cost-efficiency without compromising the integrity of construction projects.
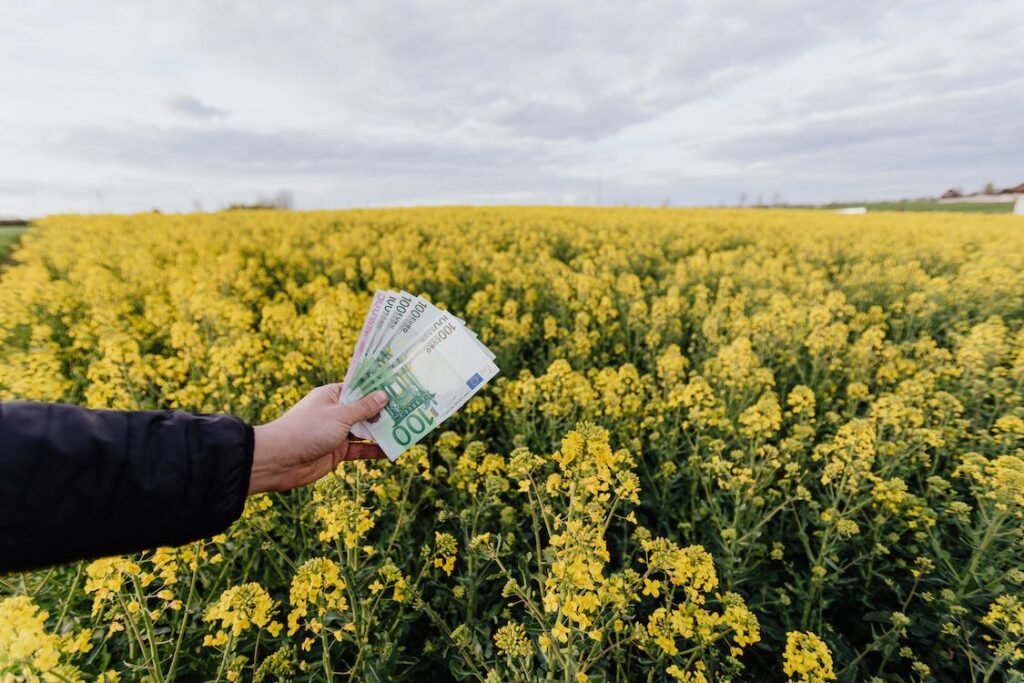
Effective Project Planning and Design
Effective project planning and design lay the foundation for cost-effective construction. Thoroughly understanding the project requirements, setting realistic goals, and developing a comprehensive plan can help identify potential cost-saving opportunities from the start. This includes accurate cost estimation, efficient scheduling, and proper allocation of resources. Adopting value engineering techniques during the design phase can also lead to cost reductions without compromising quality, such as optimising space utilisation, material choices, and construction methods.
Optimal Material Selection
Choosing the right materials is a critical aspect of cost-effective construction. The materials used in a construction project not only impact the initial cost but also have long-term implications on maintenance, repairs, energy consumption, and overall project durability. By prioritising high-quality, durable, and energy-efficient materials, builders can achieve cost savings and ensure the longevity and performance of the built environment through these areas:
- Long-Term Savings: While high-quality materials may come with a higher upfront cost, they often result in long-term savings. These materials are designed to withstand wear and tear, reducing the frequency of maintenance and repair needs. By investing in durable materials, builders can minimise the expenses associated with replacements, renovations, and unplanned repairs over the lifespan of the structure.
- Energy Efficiency: Energy-efficient materials, such as insulation, windows, and lighting systems, contribute to reducing energy consumption and operational costs in buildings. These materials optimise thermal performance, reduce heat transfer, and enhance the overall energy efficiency of the structure. Although energy-efficient materials may have a slightly higher initial cost, they lead to significant savings in heating, cooling, and electricity expenses over time.
- Cost-Benefit Analysis: Conducting a thorough cost-benefit analysis is crucial when selecting materials for a construction project. This analysis involves evaluating the initial cost, projected lifespan, maintenance requirements, energy efficiency, and potential long-term savings of different material options. By considering the life cycle cost of materials, builders can make informed decisions and choose materials that provide the best balance between upfront expenses and long-term savings.
Embracing Technology and Automation
Incorporating technology and automation into construction processes has become increasingly essential for achieving cost-effective outcomes. The advancements in construction technology have revolutionised the industry, offering a wide range of tools and solutions that significantly boost efficiency, reduce costs, and improve overall project performance:
- Advanced Software and Project Management Tools: The use of advanced software and project management tools has transformed the way construction projects are planned, executed, and monitored. These tools enable accurate project scheduling, resource allocation, and real-time collaboration among team members. Construction project management software allows for streamlined communication, document sharing, and progress tracking, reducing the risk of miscommunication, delays, and cost overruns.
- Building Information Modeling (BIM): Building Information Modeling (BIM) has revolutionised the design and construction process. It enables efficient coordination, clash detection, and visualisation of construction projects in a virtual environment. By creating a detailed 3D model that integrates architectural, structural, and MEP (mechanical, electrical, plumbing) systems, BIM minimises rework, improves coordination among different trades, and enhances overall project efficiency. Clash detection helps identify and resolve conflicts between different building components before construction begins, reducing costly on-site revisions and delays.
- Automation and Robotics: Automation and robotics have the potential to streamline construction processes, reduce labour costs, and accelerate project timelines. Automated systems can perform repetitive tasks with precision, accuracy, and speed, eliminating human error and reducing the need for manual labour. Robotics can be utilised for tasks such as bricklaying, concrete pouring, and material handling, increasing productivity and reducing dependency on manual labour. Automated machinery and equipment, such as robotic arms and drones, can improve safety, efficiency, and quality in various construction operations.
- Prefabrication and Modular Construction: Technology-driven prefabrication and modular construction techniques offer significant cost and time savings. Prefabricated components and modules are manufactured off-site under controlled conditions, ensuring high quality and reducing material waste. Prefabrication allows for simultaneous construction activities, reducing on-site labour requirements and project timelines. Modular construction facilitates faster assembly and installation of standardised building units, improving efficiency and reducing on-site labour costs.
Streamlining Construction Processes
Efficient construction processes can lead to significant cost savings. Implementing lean construction principles, such as just-in-time delivery, waste reduction, and value stream mapping, helps streamline workflows and eliminate non-value-added activities. Prefabrication and modular construction techniques enable off-site manufacturing, reducing on-site labour requirements, material waste, and construction time. Concurrent engineering, where various project components are developed simultaneously, can expedite project completion while maintaining quality standards.
Efficient Resource Management
Effective resource management plays a pivotal role in cost-effective construction. Careful planning and scheduling of labour, equipment, and materials help minimise downtime, prevent resource shortages, and optimise productivity. Tracking and monitoring resource utilisation provide insights into areas of potential improvement and cost savings. Regular maintenance and calibration of equipment ensure their optimal performance, reducing the risk of breakdowns and costly repairs.
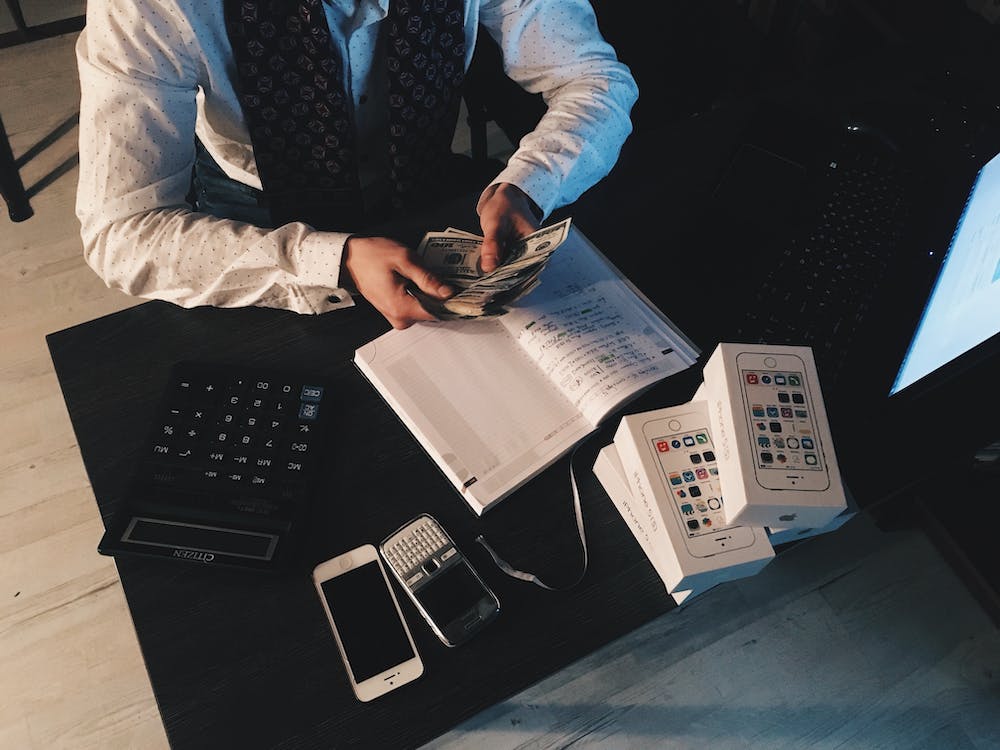
Collaboration and Communication
Open and effective communication among project stakeholders is paramount to successful construction projects. It fosters collaboration, minimises errors, promotes timely decision-making, and helps avoid costly rework. By establishing clear lines of communication and maintaining a culture of transparency, builders can enhance project efficiency, mitigate risks, and achieve cost savings. This is highlighted below:
- Regular Project Meetings: Conducting regular project meetings brings all stakeholders together to discuss progress, address concerns, and make informed decisions. These meetings provide a platform for sharing updates, clarifying requirements, and resolving potential issues in a timely manner. Regular interaction among architects, engineers, contractors, and subcontractors ensures that everyone is aligned with the project objectives and can contribute their expertise to optimise construction processes.
- Clear Documentation: Clear and comprehensive documentation is essential for effective communication and minimising misunderstandings. This includes detailed project plans, specifications, contracts, and change orders. By documenting project requirements and agreements in a clear and concise manner, potential conflicts and disputes can be avoided. Documented instructions and guidelines help ensure that all parties have a common understanding of expectations, reducing the likelihood of errors and rework.
- Timely Sharing of Information: Timely sharing of information is crucial for seamless collaboration. Architects, engineers, contractors, and subcontractors should regularly communicate updates, changes, and progress to keep all stakeholders informed. Leveraging digital platforms and project management software allows for efficient sharing of documents, drawings, and other project-related information. This reduces the risk of miscommunication, delays, and errors that can result in costly rework.
- Collaboration Platforms and Project Management Software: Collaboration platforms and project management software provide tools and features that facilitate effective communication and document sharing. These platforms allow stakeholders to collaborate in real-time, track project progress, and manage workflows efficiently. Features like shared calendars, instant messaging, and centralised document repositories enable seamless collaboration and promote transparency among team members. By utilising these digital tools, construction professionals can streamline communication processes, reduce delays, and improve overall project coordination.
- Strong Relationships with Suppliers and Subcontractors: Fostering strong relationships with suppliers and subcontractors can lead to cost savings and favourable terms. By maintaining open lines of communication, builders can negotiate competitive pricing, bulk discounts, and favourable payment terms. Suppliers and subcontractors who understand the project requirements and constraints are more likely to offer value-engineered solutions, suggest cost-saving alternatives, and provide efficient delivery of materials and services.
Monitoring and Quality Control
Implementing robust monitoring and quality control processes throughout the construction project is essential for cost-effective outcomes. Regular inspections, quality audits, and adherence to industry standards ensure that work meets the required specifications and minimises the need for rework or corrections. Utilising technology-driven tools like drones and sensors can facilitate accurate monitoring of construction progress, detect potential issues early on, and improve overall project quality. By maintaining a focus on quality control, the risk of costly errors, delays, and customer dissatisfaction is mitigated.
Continuous Improvement and Learning
Cost-effective construction strategies are not static; they evolve with advancements in technology, best practices, and lessons learned from previous projects. Encouraging a culture of continuous improvement and learning within the construction team enables the identification of areas for optimization and innovation. Regular project debriefs, feedback loops, and post-project evaluations help identify successes and areas for improvement, allowing for the refinement of cost-effective practices. Staying updated on industry trends, attending professional development programs, and leveraging industry networks contribute to the ongoing enhancement of construction strategies.
Achieving cost-effective construction without compromising quality requires a proactive and holistic approach. By implementing effective project planning, optimal material selection, embracing technology, streamlining processes, efficient resource management, fostering collaboration, monitoring quality, and embracing continuous improvement, builders and construction professionals can maximise efficiency, control costs, and deliver high-quality projects. Balancing cost savings with quality outcomes not only enhances the reputation and profitability of construction companies but also fosters client satisfaction and long-term success in the competitive construction industry.
Incorporating these cost-effective strategies into construction projects requires careful consideration of specific project requirements, local regulations, and industry standards. By prioritising efficiency and quality, builders can achieve optimal results while maintaining a competitive edge in the construction market.
As the construction industry evolves, embracing software like Wunderbuild can significantly contribute to streamlining processes and ensuring project efficiency. Wunderbuild is not just a project management tool; it’s a comprehensive construction management platform designed with the needs of the construction industry in mind. With features like effective job management, and lead management, Wunderbuild simplifies project planning and enhances real-time collaboration. It’s an ideal partner for builders seeking to implement cost-effective strategies that don’t compromise on quality. From initial estimates to the final completion, Wunderbuild ensures all project aspects are covered, promoting efficiency, reducing expenses, and maintaining the quality of your projects. To learn more about how Wunderbuild can optimise your construction processes, discover more here.